Vacuum Casting Service
Low-Cost Prototype Production
There are many prototyping options, but none of them is as fast, accurate, and affordable as vacuum casting. This manufacturing process offered by the LT century team allows you to make identical designs in small quantities.
Vacuum casting is a production technique used for manufacturing a small volume of functional parts. It is a three-step process that allows accurate duplication of a model using a silicone mold. In LT Century, our vacuum casting services can save you time and money compared with other methods like CNC machining.
Industries Include:
- Automotive
- Engineering
- Electronics
- Manufacturing
- Aerospace
- Energy
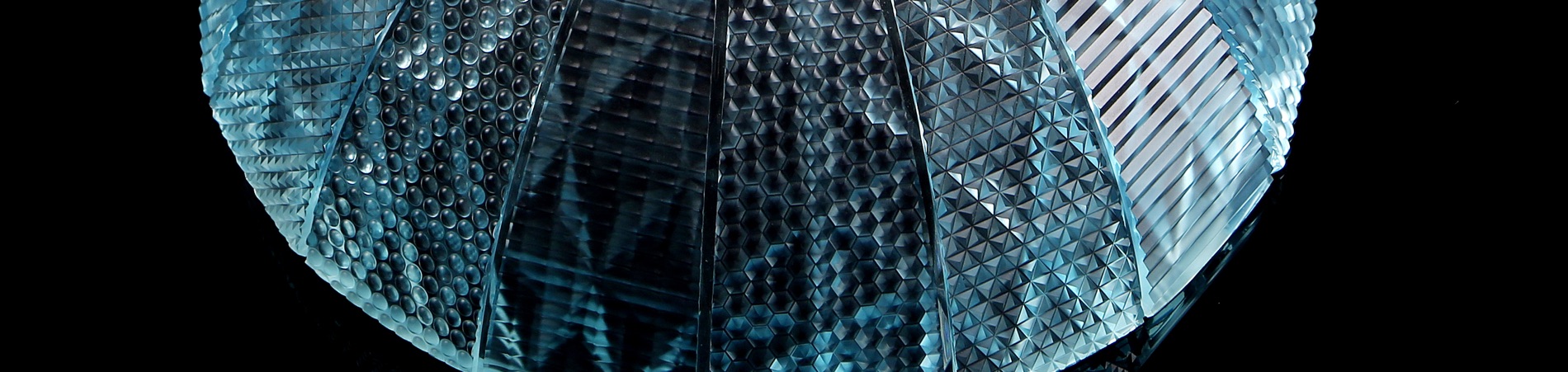
Fast and Efficient Vacuum Casting Services
Looking for a quick and efficient way to make your prototype?
Vacuum casting is the right manufacturing technique for your project. Although there are multiple steps involved in the process, it is easy and straightforward. Prototypes are done in a matter of days and not weeks. The vacuum casting process involves three steps: creating the master pattern, producing the mold, and casting copies.
Step 1. Creating the Master Patterns
The vacuum casting process begins with creating the master model. It’s made by converting the CAD files into 3D representation using CNC machining or 3D printing like SLA or SLS. If our customers prefer to supply their patterns, we at LT Century would gladly accommodate it. These patterns, however, should be able to withstand 40 degrees temperature.
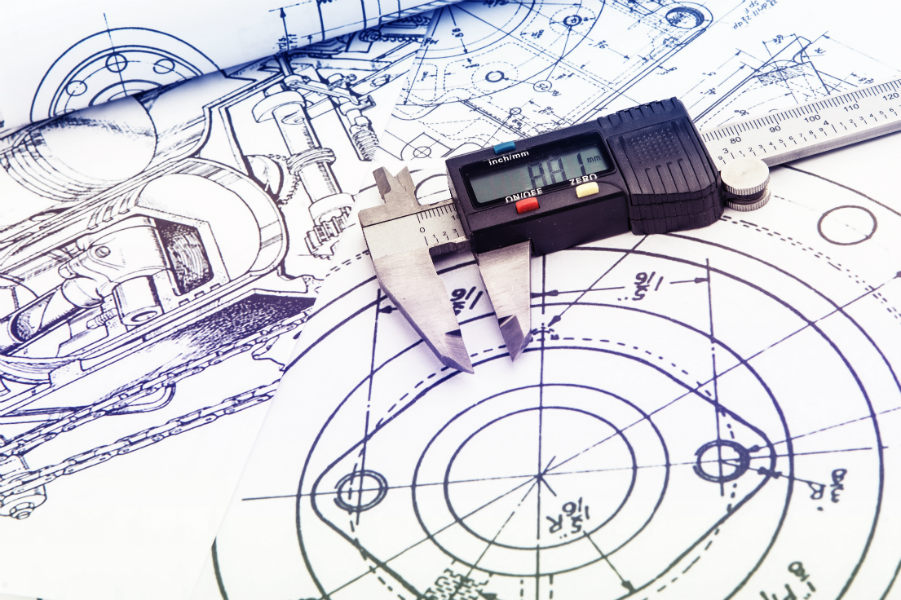
Step 2. Making the Mold
Creating the mold is done using liquid silicone. The silicone material is injected in the casting box with the master pattern inside. The main idea is for the casting material to surround the master pattern and create an impression. It is cured in an oven for more than 16 hours.
Once the curing process is completed, the mold is cut open and the master pattern removed. What is left is an empty cavity with the shape of the master pattern.
Step 3. Producing Copies
The last step in vacuum casting is creating copies. In this step, the resin is poured into the empty copy to make a replica of the original. It allows for two or more resins to manufacture prototypes and the silicon mold can make 20 or more copies from the master model.
The difference between vacuum casting and other techniques is the vacuum casted parts are high-quality. It renders the parts suitable as a series of final components in small quantities, for function testing, and marketing purposes. It can produce parts without air packets that could compromise its integrity.
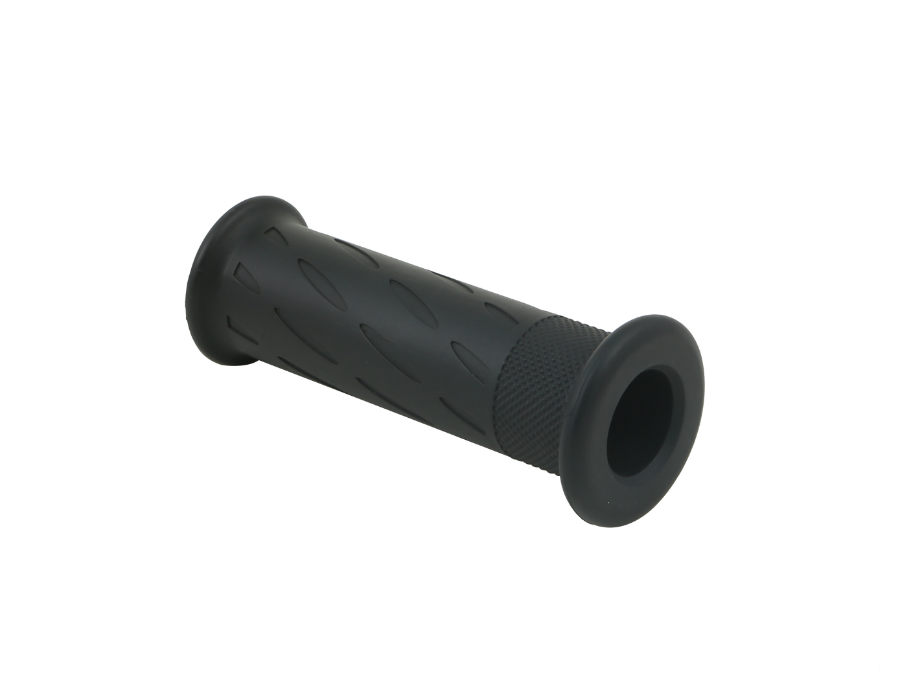
Applications of Vacuum Casting
LT Century can make the silicon molds ready within days. It can make up to 50 copies of parts made from high-quality polymer. It’s a perfect low-cost manufacturing technique. We recommend vacuum casting to manufacture prototypes for proof of concept, visual aids for presentation, and design testing.
The parts made from vacuum casting are accurate, durable, and detailed. We can manufacture them using affordable polymers that need no further processing. That translates to cost savings because there are no finishing treatments needed on the finished parts.
Here are some applications of vacuum casting:
- Proof of concept
- Product testing
- Low volume manufacturing
Vacuum casting is used by a wide range of industries that includes energy, aerospace, manufacturing, electronics, engineering, and automotive.
Vacuum Casting Materials
There are hundreds of casting polymers that are commercially available that fit the requirements for vacuum casting. They have the surface texture and hardness that you might be looking for. You can also make parts of different transparencies. Whether it’s translucent, transparent, or opaque, it all depends on how these parts will be used.
At LT Century, you can choose from any of the following materials:
- Rubber-like polyurethanes
- PE/PP-like polyurethanes
- ABS-like polyurethanes
The dimensions of the finished vacuum cast parts will depend on the accuracy of the master pattern, the types of casting material, and the geometry of the design. Generally, the shrinkage rate of these finished parts is not higher than 0.15%.
Benefits of Using Vacuum Casting
Take a look at the benefits vacuum casting technique at LT Century
- High Precision – The silicon mold is faithful to the master pattern. Vacuum casting has high fidelity, with the intricate details translated into the finished part.
- High-Quality Parts – The wide range of resins available for vacuum casting use allows you to choose the right material for the design with the right amount of hardness: rigid or flexible and final appearance. You can have the finished part with colors and the right transparency. You can also create over moldings or have painted finishes.
- Saves Time and Cost – Using silicone, an affordable mold makes lower the price compared to other forms of tooling. It is more valuable than 3D printing because you can make ten parts. On top of it all, it only takes 7 to 10 days to complete around 50 parts.
Request a Free Quote Today!
Receive a free quote for your vacuum needs within 24 hours when you contact LT Century today. Our Sales staff can talk to you in several languages and will answer any questions you have.