Vacuum casting has emerged as one of the vital tooling processes in the manufacture of prototypes before large-scale production is rolled out. There is a wide range of vacuum casting methods that are used in the manufacturing of parts from polymers and metals.
The process of vacuum casting is quite simple and straightforward as it utilizes rubber silicon tools. For this article, we are going to inform you about what the process truly entails.
What is vacuum casting?
The initial process begins with the preparation of the master plan. This is done through the Stereolithography process or using CNC machines. The process is quite accurate and fast producing identical parts or designs in small quantity, saving you both time and money, allowing you to make changes in the original design, ensuring that the needs of our clients at LT Century are fully met.
In the first phase, the liquid PUR is inserted into the mold that is, in turn, held under vacuum, which ensures that the design material has no porosity, which allows it to freely flow into the mold cavity without the restrictions of air pressure.
The PUR is positioned above the mold, so as it’s poured, it will flow underneath the forces of gravity, forcing it to move upwards. The runner design system ensures the cavity is wholly filled evenly.
Wait a few minutes to ensure the cavity is filled with the vacuum equalized. Completely seal the mold allowing for curing time that can last anywhere between 45-minute to one hour. In the 2nd phase, the mold parts are removed, and the excess materials are removed.
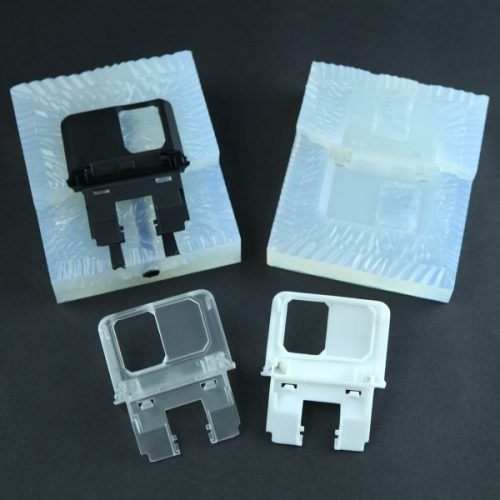
vacuum casting products*
When to use the vacuum casting process
Where there is the production of a prototype, vacuum casting services should be your go-to tooling process. The casting process provides design solutions where machined parts need to have a more exceptional level of detail and excellent quality surface.
Materials used in the vacuum casting process
When it comes to vacuum casting services, there is a wide range of materials that designers can use based on thermal properties, end-product physical and mechanical properties. Most of the materials used are:
- Rubber- They have a high degree of flexibility, making it ideal for producing gasket and seals as its tear-resistant. Rubber is widely used in the manufacture of replicated parts, and it’s also cheap and easily available
- ABS has high rigidity and strength
- Glass-filled Nylon and Polyamide have a higher degree of rigidity
- High-Density Propylene or Propylene has high elasticity
- Polycarbonate is resistant to both high and low temperature giving it a perfect translucent nature
- PMMA is resistant to high heat as well as being shock-resistant
Benefits of using vacuum casting services
- It produces end-products of high quality and has higher dimensional accuracy.
- The products have excellent aesthetic appeal with quality surface finishing; it also allows the addition of color pigments in the vacuum chamber and resins giving you parts and product unique and colorful color.
- It makes the entire vacuum casing process clean, economical, and eco-friendly.
Reference
*Image from https://www.ecplaza.net/