Altering the surface of a completed part to achieve a certain attribute is a tall order in manufacturing finished products. Hence, finishing services are an integral part of the manufacturing industry. There are plenty of reasons why it is needed, including aesthetics, solderability, adhesion, resistance against chemical, wear or tarnish, electrical conductivity, hardness, removal of a flaw, and better control of surface friction. In other cases, finishing services are employed to salvage or repair a damaged part and to restore the original dimensions of a part.
Whatever the reason, there is an appropriate surface finishing that will serve its purpose. Here are the choices for finishing services that you can select from.
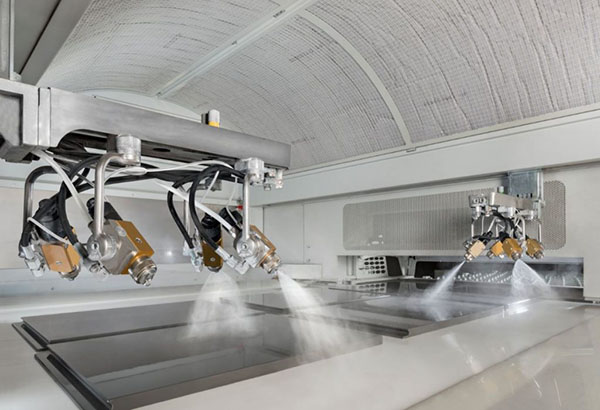
Spray painting*
1. Spraying
It is a simple painting technique that involves using a spraying device that is usually powered with compressed air to paint a surface with a selected kind of coating. There are many coating materials available, including ink, paint, varnish, and a host of other types.
The spray guns and airbrushes used in this type of finishing services are denoted by their sizes and spray patterns. In addition to these devices, you can also find spray booths in automotive shops. It is pressure-controlled and done in a closed environment to create the ideal airflow, temperature, and humidity that will create a perfect finished.
2. Silk Screening
This finishing is meant to place a logo, part number, serial number, or any text or image directly on the completed prototype or part. It is the best alternative because you can use it with other finishing services. It involves using a fine mesh fabric that is stretched over the top of the part. Nowadays, silk screening is carried out by professional equipment instead of being handmade. It creates more intricate designs and unlimited color applications.
3. Plating
Plating is another finishing process that involves depositing metal into a conductive surface. It renders many desirable properties to the part aside from being decorative. Desired properties like solderability, resistance, friction reduction, wearability, and many more are added to the part through plating. Although this is an older process, modern technology has added a new dimension to the plating. It is now possible to plate the object up to an atom level in nanotechnology.
4. Anodizing
This finishing service is meant to increase the thickness of the natural oxide layer on the surface of the metal parts. It is commonly applied to substrates of aluminum alloy but is also applicable to zinc, titanium, zirconium, niobium, and others. The process involves using electrolytic passivation and is done to achieve properties like wear and corrosion resistance, better adhesion, and for aesthetics.
5. Laser Etching
Laser etching and engraving belong to the general category of laser marking. Both are similar as they produce a permanent mark as the laser removes the material from the surface of an object. It is used in any material as an ideal solution for parts that need permanent marks as part of identification and traceability. Laser etching is employed to mark date and time stamps, serial numbers, logos, barcodes, and other manufacturing information.
6. Polishing
Polishing is a finishing service that involves the use of an abrasive material attached to a wheel. It creates a more aggressive finishing process the remove the surface material from the part, resulting in a more polished and brighter finish.
You can use all these finishing methods and more on metal prototypes or machined parts to produce the kind of surface that you want.
Reference
*Image from https://www.mpsmachines.co.uk/