Vacuum casting polyurethane has become an essential process for the production of a small and identical number of polyurethane prototypes products or parts before large-scale production is rolled out.
Vacuum casting is a highly modern and versatile tech that has the capabilities of creating a wide range of cast nylon and polyurethane (PU) resins and replicate, replace or create engineering polymers for end-use parts or prototypes.
The process is suitable for low volume production, where injection molding is not feasible or profitable. Normally in vacuum casting, a single mold can produce up to 50 identical parts/products before re-tooling is required.
One of the critical steps in vacuum casting is the creation of the mold. Typically, at LT century, this is usually done at RTV (room temperature vulcanization) with the master model being created from silicone rubber.
The master model is usually made via 3D printing from a digital model of CAD (computer-aided design). But if a client wants an identical part/product, the prototype is made from a silicone rubber mold.
Molds created from vacuum casting polyurethane can reproduce up to more than 50 parts, making it cost-effective.
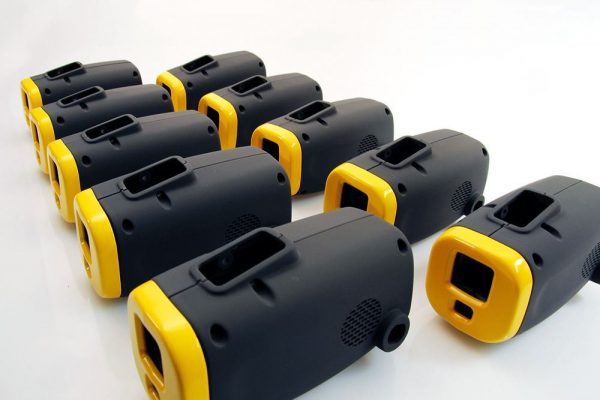
vacuum casting products*
Key Consideration of Design of Manufacturing and How it can Affect our Projects
Design for manufacturing, whether large or small scale, can take a lot of your time before you finally get It right. Optimization of all the process and procedures to get an excellent end-product requires a lot of logistical issues which can be quite tasking.
Well, to make things easier for you, we are going to narrow it down into the main layers when creating parts using vacuum casting polyurethane. These are some of the primary specifics that you need to pay special attention to.
Choice of Material
DFM gives our designers at LT century a great deal of control over the whole project, depending on the clients’ contract we can sometimes overrule his/her preferred choice of material if we feel that we can find something that works better for our clients.
Selecting the right polymer should be at the top of your list, a case study that is carried out will determine which is the best material that should be used for your project.
Mold Gates
The mold gate is the central part where everything happens as the runner system transports the molten material to the mold. If you have the right length, then the flow of the material will be exactly as intended.
For mold gates measurements is everything, thus its important that designers check and re-check the numbers to ensure everything is right.
Reinforcements
A few vacuum caste parts will require additional heftiness due to their unique designs; the added support is also referred to as reinforcements that will fortify and make your end-product stronger.
Most of the time, they make the walls of your product/part thicker. Reinforcements also reduce the tension stress, but accurate projections should be made to get the exact mounting points, which can be quite tricky, but it’s doable.
Reference
*Image from https://www.materialise.com/