Many industries across the world heavily use sheet metal manufacturing and production. Almost all manufacturers rely on the use of metal parts and components in the most complex devices on virtually all niches of the market. In every industrialized location, there is always someone who relies on metal parts, specialized components, intricate frameworks, or single pieces of equipment that can’t be developed without sheet metal manufacturing. The versatility of metal plays a role in large structures and support systems as well as in micro digital assemblies.
Explaining Sheet Metal Manufacturing
Sheet metal manufacturing is the sum of a series of individual processes that allow the formation of designated metal sheets according to planned specs on behalf of a developer. Special tools are used or created to perform a specific task or defined applications. The conjunction of these procedures always includes the use of known technologies such as cutting lasers for specific tasks such as press brake forming. The endgame is to deliver a sheet of metal that is created for a special type of project. Engineering and design play significant roles in the creation of each part. The following are some of the procedures used in the creation of metal sheets projects as they work today:
Choice of Materials
In the early stages of any project, this is probably one of the most critical steps to take. Developers must choose the material they are going to work with by following the specs of their projects. All metals have different types of complexity to work with. Some are easier to handle than others. As such, choosing the right metal for a project requires the proper study on behalf of the designers and engineers. Having a clear idea of what we need will make the information on the cost of our project more accurate, and it will make it more functional time-wise.
Bend and Shape
Bend in sheet metal manufacturing is a procedure that transforms flat metal sheets into something new using tools, such as press brakes. Some of the most common bends using worldwide are the U bends, and the V bends, but most projects go for customized forms. A shape is a procedure closely related to machining and stamping. Bend is more used since it is not as complex. Shape, on the other hand, calls for the use of more unique tools since the task it’s more delicate and requires a lot more precision. Some of the most well-known procedures are done using rotary elastomer tools that make easier the creation of new shapes in delicate surfaces. Rougher means are used on sturdier materials such as punching since they are mostly done using CNC precision machining.
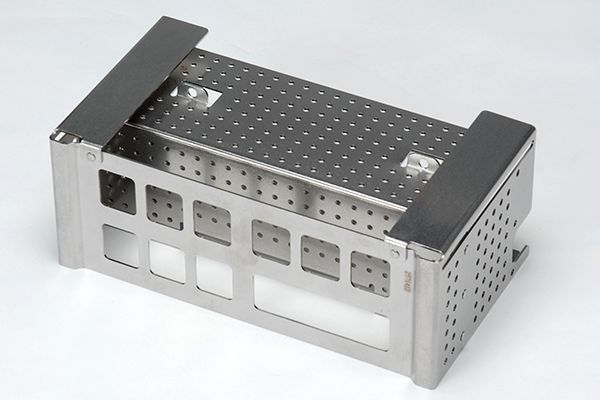
sheet metal fabrication*
Cut and Trim
Cutting a sheet of metal might not look as complicated as it seems, but given the amount of precision needed in the build of many devices, cutting procedures demand a series of specific tools aimed at making the work on any project more precise. A lot of technology for cutting and trimming metal already exists. The new developments on this specific field are aimed at making cutting jobs faster or to deal with studier materials. The number of devices available in the market is aimed at the different levels of craftsmanship as well as the size of the project. Newcomers and professional alike can find something that suits their ideas.
One of the most requested tasks in the market is custom cutting and trimming sheets of metal made of special alloys. Another popular niche is the work required for precious metals. The most expensive line of work will always be cutting and trimming hard materials since it usually calls for specialized equipment such as heat lasers. The result with this high-end tool is often very precise, accurate and efficient. Since the task is mostly performed by automatic devices the margin for error is minimal, and it’s also one of the most versatile procedures out of the list given the number of shapes it can deliver in short notice.
Join and Connecting
A lot of manufacturing projects require more than a single sheet of metal. These builds also require welding, assembly and the connection of some individual parts to get a product ready to go. Some of the most popular procedures used to create completed parts include riveting metals, the use of adhesives, and brazing. More specialized means of connection can be used, but these procedures are usually customizations or alterations of existing procedures for very specific tasks.
Finishes
When a sheet of metal is worked on using the procedures we have previously mentioned it will require a finish stage where the project is completed by applying a coat of paint or even packaging. Some of the most common finishing procedures are silk screening, oil painting, powder coatings, and customized special treatments for surfaces. Most of these procedures are handled by automated machinery that gives finishing treatments an industrial touch to these metal components and seals their unique properties. Finishing a product means shutting in what makes it work and exposing their working conditions and readiness to be used.
Reference
*Image from on https://midlake.com