Sheet metal is a commonly used and versatile material in the manufacturing industry. It is made from steel, brass, copper, aluminum, tin, nickel and other precious metals. The pure form of this material is in sheets with the thickness that can range from thin foil to a heavy plate. It can take a variety of forms and shapes, but the most common are in flat sheets are can be embossed, ribbed, etched, corrugated and even perforated.
Advantages of Sheet Metal
Depending on its application, sheet metal has many advantages over its contemporaries and even to the non-metal alternatives as well. First off, in comparison to machining, sheet metal has generally lower cost of material.
This is because instead of starting the process with a block of material, which much of it will be machined away, this material is in the flat sheets. You only need to buy just the size that you need and will use. What remains of the sheet can still be used while in other materials, the shavings that you removed after machining has to be recycled.
Many technological advances have made sheet manufacturing more effective and quicker. When sheet metal manufacturing is automated, you can produce the parts directly from CAD models. In this technology, it uses a wide range of materials and techniques to create a product or shape finished components. Because of the demand for mass production, the fabrication of sheet metal is scalable. The first pieces may be costly, but the subsequent production will reduce the cost significantly. As the production volume increases, the cost of production will drop considerably as compared to when you are using a subtractive method like machining.
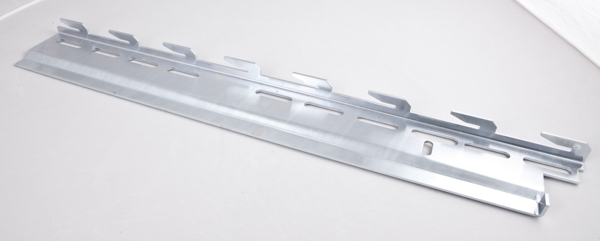
sheet metal*
Manufacturing Processes Involving Sheet Metal
Initially, sheet metal starts as a flat sheet, but this material is malleable and can be shaped into many different forms to meet the requirements. The primary methods of developing this material are by bending the sheet metal along a single axis.
More techniques that are sophisticated can shape the metal into multi-axis forms including hot and cold forming methods. This includes deep drawing, stamping, spinning, and hydroforming. Most applications for these forms are in creating the body panels for vehicles, and a complex formed objects like the soda can and the modern sink. These processes are repetitive, doing the same process repeatedly to change the shape of the metal slowly.
For shaping the metal along the single axis, most of the processes include shearing or cutting the sheet and punch press. Using the punch press is ideal when you want to make the suitable parts faster as it can operate a hundred stroke per minute. CNC laser cutting is the latest technological advancement, and the use of oxygen, helium, carbon dioxide can burn away the metal and give clean finishing. Another process called photochemical machining uses CAD-generated stencils to make a pattern on the sheet and chemically removed the unwanted part.
Hemming is also another method employed on sheet metal and involves rolling the edges for stronger and smoother edges. Another hemming technique is called curling to eliminate the sharp edges or to serve a specific purpose like putting hinges in the case of a door.
Materials Use in Sheet Metal Manufacturing
There are varieties of metals and metal alloy that can be formed into sheets and in fabricating parts from sheet metal. In choosing the material for its manufacture, the factors to consider are the needs of the application, formability, corrosion resistance, strength, weight, cost, and its malleability. Some of the most popular materials for sheet metal manufacturing includes stainless steel, cold rolled steel, pre-plated steel, aluminum, titanium, copper, and brass.
Sheet Metal Fabrication
This is a non-additive, non-subtractive process. Sheet metal fabrication begins with the flat material, and this material maintains its thickness throughout the process. If it needs to be thick, several layers are welded together. However, this process is costly and seldom used. Sheet metal fabrication is one of the technological advancements that is seen more in the field of aerospace, medicine, electronics and many more.
The processes that involve metal fabrication includes cutting, bending, assembling, welding, machine design, powder coating, turret, and laser automation. All these methods require precision and has no room for error. After this, the sheet metal fabrication product will undergo finishing which is a combination of bead blasting, soda blasting and sandblasting.
Sheet metals are now used to make components and parts for nearly every industry today. These decorative, durable and workable sheet metals had many applications and based on your requirements and specifications, a specialized technique can form them into unique and complex shapes. In LT Century, you can have the right method of production for your sheet metal based on the design, requirements and material preference. They are ready to manufacture based on the demand and size of the project.
Reference
*Image from on https://www.monti-inc.com