Die casting could be a preparation that’s characterized by constraining liquid metal beneath tall weight into a form depth. The shape of depression is made utilizing two solidified device steel items that have been machined into shape and work so also to an infusion shape amid the method. Most passes on castings are made from non-ferrous metals, particularly zinc, copper, aluminum, magnesium, lead, pewter, and tin-based combinations. Depending on the sort of metal being cast, a hot- or cold chamber machine is utilized. The die casting equipment and the metal passes on speak to huge capital costs and this tends to restrain the method to high-volume generation. Make of parts utilizing pass on casting is generally basic, including as it were four primary steps, which keeps the incremental fetched per thing mold. It is particularly suited for a huge amount of little- to medium-sized castings, which is why pass on casting produces more than any other casting preparations.
Tooling/Mold Of Die Casting:
Two passes on are utilized in kick the bucket casting; one is called the “cover pass on half” and the other the “ejector kick the bucket half”. Where they meet is called the separating line. The ejector kick the bucket contains the ejector pins and more often than not the runner, which is the way from the sprue or shot gap to the shape depth. The cover container is secured to the stationary, or front, platen of the casting machine, whereas the ejector kicks the bucket is joined to the mobile platen. The shape depth is cut into two depression embeds, which are partitioned pieces that can be supplanted generally effortlessly and jolt into the kick the bucket parts.
Disadvantages Of Die Casting:
The most drawback to kick the bucket casting is the exceptionally tall capital taken a toll. Both the casting gear required and the passes on and related components are exceptionally exorbitant, as compared to most other casting forms. Hence, to create a pass on casting a financial handle, an expansive generation volume is needed.
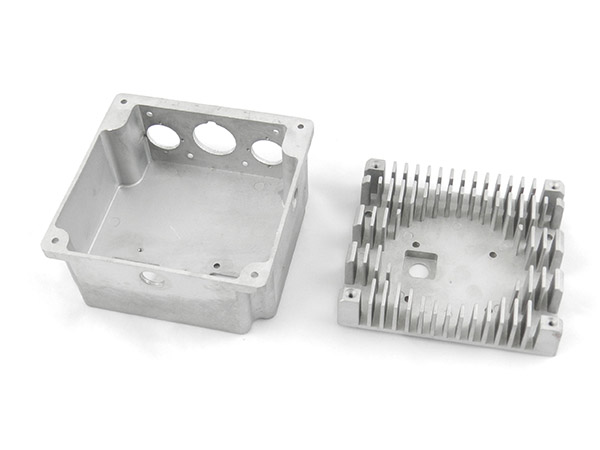
aluminum die casting in LED lighting industries*
Die Casting Advantages:
Quick generation rates. Diminishes or disposes of auxiliary machining operations. The casting of mold ease metals. Casting malleable quality as tall as 415 megapascals (60 ksi). More slender dividers can be cast as compared to sand and lasting form casting (roughly 0.75 mm or 0.030 in).
The Process Of Die Casting:
The taking after is the four steps in conventional kick the bucket casting, moreover known as high-pressure kick the bucket casting, these are moreover the premise for any of the kick the bucket casting varieties: pass on the arrangement, filling, launch, and shakeout. The passes on are arranged by splashing the form depth with oil. The grease both makes a difference control the temperature of the pass on and it moreover helps within the evacuation of the casting. The passes on are at that point closed and liquid metal is infused into the passes on beneath tall weight; between 10 and 175 megapascals. Once the form depth is filled, the weight is kept up until the casting sets. The passes on are at that point opened and the shot (shots are distinctive from castings since there can be numerous cavities in a kick the bucket, yielding numerous castings per shot) is catapulted by the ejector pins.
Reference
*Image from https://eurobalt.net/