Rapid prototyping service is the fabrication of a model, assembly, or physical part with the use of 3D computer-aided design (CAD). The process is completed with the use of additive manufacturing. This is where the design matches the proposed finished product, a high fidelity prototype.
How Does Rapid Prototyping Works
Rapid prototyping includes different types of manufacturing technologies, but most uses layered additive manufacturing. Other techniques make use of RP that includes casting, extruding, high-speed machining, and molding.
Although additive manufacturing is the most widely used rapid prototyping process, some use conventional methods to create prototypes.
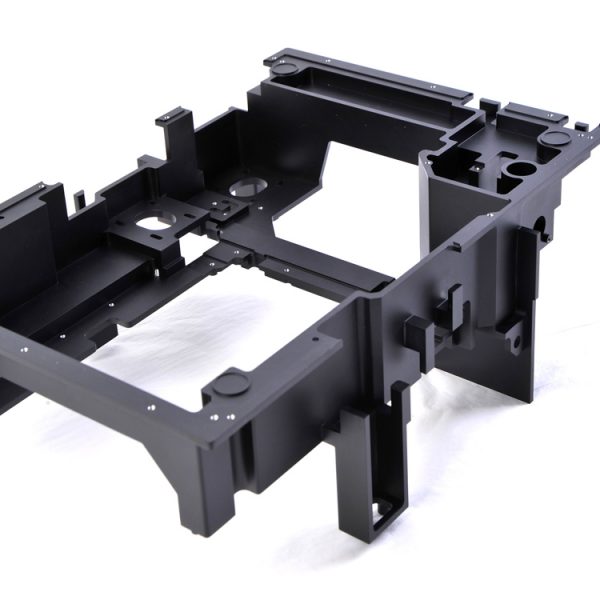
rapid prototyping products*
These processes are as follows:
Subtractive
In this stage, a block of material is cut to generate the desired shape with the use of turning, milling, or grinding.
Compressive
This process involves forcing a liquid or semi-solid material into the desired product before it solidifies, like compressive sintering, casting, or molding.
Different Types of Rapid Prototyping Services
Stereolithography (SLA) or Vat Photopolymerization
In 3D printing, the first successful process is SLA. This method is fast and cheap and uses a photosensitive liquid that solidified layer-by-layer with the use of a computer-controlled UV light.
Selective Laser Sintering
The process is used for both plastic and metal prototyping. This method makes use of a powder bed to create a prototype one layer at a time with the use of a laser to heat and sinter the powdered material. But, the parts are not as strong as with Stereolithography, the surface of the end product is not smooth and may require additional work to complete.
Fused Deposition Modelling/ Material Jetting
This costly, simple to use method is usually used in non-industrial desktop 3D printers. This process uses a spool of thermoplastic filament, which includes melting in the printing nozzle barrel before getting the resulting liquid plastic that is presented layer-by-layer based on a computer deposition program. The result is not yet as good as expected. It has poor resolution and weak. This method improves fast and remains cheap, which makes it ideal for the enhancement of the product.
Selective Laser Melting / Powder Bed Fusion
The powder bed fusion is preferred for manufacturing high-strength complex parts. This process is usually used by the automotive, medical, defense, and aerospace industries. SLM uses a fine metal powder that involves the melting of metal powder in a layer by layer manner to develop either prototype or production parts with the use of an electron beam or a high-powered laser. Some of the commonly used materials in powder bed fusion are titanium, stainless steel, cobalt chrome alloys, and aluminum.
Laminated Object Manufacturing / Sheet Lamination
The less costly process is less complicated as compared to SLS or SLM, but it does not need specially controlled conditions. This process involves building up a series of thin laminates that are cut accurately using laser beams or other cutting devices to produce the CAD pattern design. The layer is delivered or bonded over the old ones until the part is complete.
Rapid prototyping service varies depending on the type of industry. It is used in manufacturing parts and scale models for the car industry. It is also applied in other industries like aerospace and medical.
Reference
*Image from https://www.alibaba.com/