Injection molding is the best and very popular manufacturing process which is suitable for the production of parts in large volume. This is the reason it is mostly used for mass- production processes. So, this is suitable for requirements like same parts must be produced in thousands or in millions.
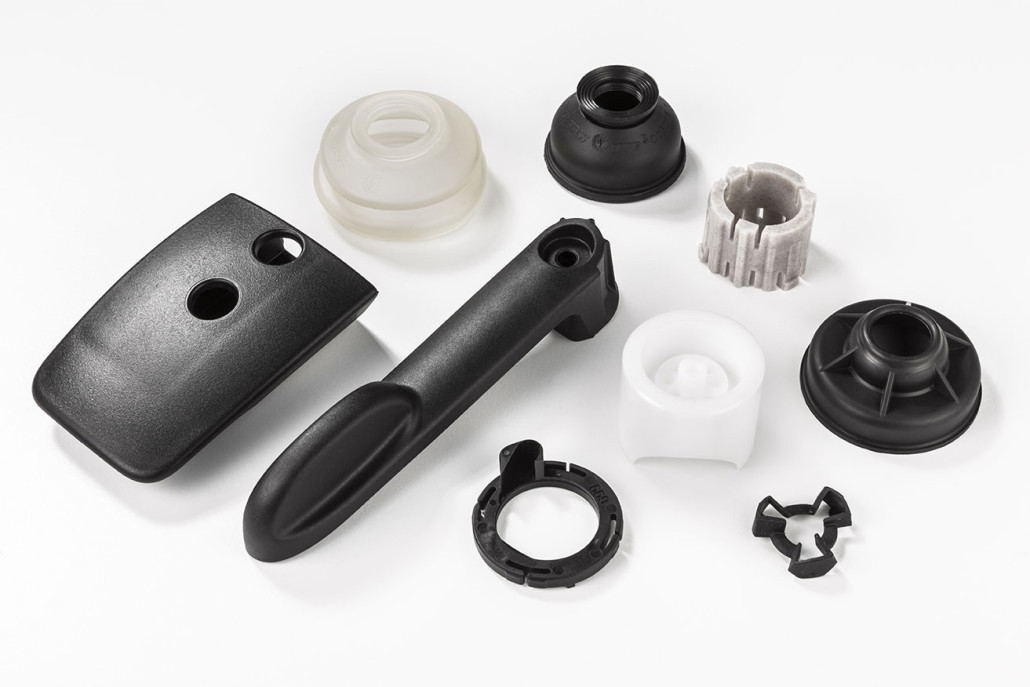
plastic injection mold parts*
Why Injection Molding:
The main advantage of this injection molding is that it’s ability to scale for mass production. Initially there will be considerable costs for manufacturing of parts using injection molding. Once this is paid, further manufacturing cost for each unit will be very low. So, it is possible to save lot of money using this injection molding in manufacturing. Along with this as the volume of the manufacturing increases, price still drops significantly.
Along with the saving cost there are many other advantages of this injection molding. The wastage or scrap is really low in this type of manufacturing. So, compared to traditional manufacturing process, for example CNC machining these results in low scrap rates. CNC machining usually cuts away significant amount of original sheet or plastic. There will be wastage coming out of the injection molding. Waste comes consistently from runners, sprue, gate locations, and in some cases parts leaking from cavity.
Sprue is nothing but the channel which guides the melted plastic from injection molding nozzle and which goes to the entry point. This is a separate part from the mold tool. The runner is nothing but the system of channels which meet up with the sprue. This is the part of the injection mold tool. This helps in guiding the molten plastic into part cavities inside the mold tool. Gate is nothing but a part of the channel which comes after the runner.
If we consider the thermoset material for example epoxy resin which can cure once it is exposed to air, this will burn if one tries to melt it after curing. But thermoplastic material is nothing but a plastic material which is possible to melt, cools, and also solidifies and then can be melted again without burning.
So, when the thermoplastic is used in injection molding, the scrap can be recycled and used again. So, this can be performed right in the factory itself in many cases. They usually grind these runners and sprues along with any reject parts. Later this material which has undergone grinding will be added along with the raw material and injected to the injection molding.
This material is called as re-grind. So, there will be quality control department in the manufacturing industry which keeps an eye on this recycled material. They will put limits on the amount of regrind which must be used for the press.
In case if they have too much of this material they usually sell it. Usually this regrind can be used for the manufacturing of low quality parts from which there is no expectation of high performance properties.
Injection molding is highly repeatable. The second part of production is exactly similar to the first part done. This is the best thing about the injection molding which helps in maintaining consistency. So, it is easy to maintain brand consistency using manufacturing through injection molding. Other benefit is it becomes easy to maintain part reliability along with consistency in case of high volume production through manufacturing using injection molding.
Injection Molding: Pints to keep in mind
There are few things which need to be considered before starting the manufacturing using injection molding.
Financial Considerations:
There is a necessity of huge initial investment in case of injection molding manufacturing. So, one must ready for this initial investment. This is the crucial point which must be considered.
Quantity of production:
Injection molding is definitely a cost effective way for manufacturing parts in high quantities. So, decide about the parts which you need to be manufactured. If the volume is more important then choose this way of manufacturing. Otherwise, if the volume is less and quality is of high importance then go for mold which can bring high quality products.
Considerations in terms of design:
There are requirements like from day one parts must be designed through injection molding. Then one must think about simplifying the geometry and lessen the number of parts which must be produced.
The design of the mold must be accurate in case of injection molding manufacturing. This will avoid the defects which may occur during the actual production. There will be some common defects which usually happen when designing injection molds. So, one must do some homework and rectify and reduce these mistakes. When doing the manufacturing in large numbers, this will cause high losses if it is not rectified at early stages.
Cycle time should be minimized as much as possible. One must involve hot runner technology as well. Small changes made can matter a lot in case of injection molding manufacturing and they can help to reduce few seconds in cycle time. So, this reduced cycle time will help in making huge savings in the manufacturing.
Reference
*Image from on http://www.mpeplastics.com