For those who have purchased new cars in recent years or exchanged, you’ll notice that your new vehicle has a more plastic feel to it than metal. I know am not the only one wondering why this is so? A lot of us think that the use and application of plastic injection molding have been on the rise especially in the motor industry is due to its affordability and cost-effectiveness.
Well, for your information this is not only limited to the automotive sector; it’s used across the board in different manufacturing processes. Plastic injection molding is used to produce high-quality components and parts efficiently and effectively.
In this post, we are going to discuss various reasons that have caused this shift from metal parts to plastics.
Weight
To put things into perspective, let’s take for example a bullet vest; they were mostly designed using metal tools a fact which had a significant impact on the movement and maneuverability. The same was applied in riot control gear and guns which affected the work of law-enforcement agencies.
Well, in modern-day; most equipment used by security enforcements use tools lined with an impenetrable polymer that can withstand bullet impact without hampering the movement of the person.
The same principle applies to other types of products and equipment such as cars, kitchen appliances, and electronics just to name a few; they are all lighter and very easy to handle and operate.
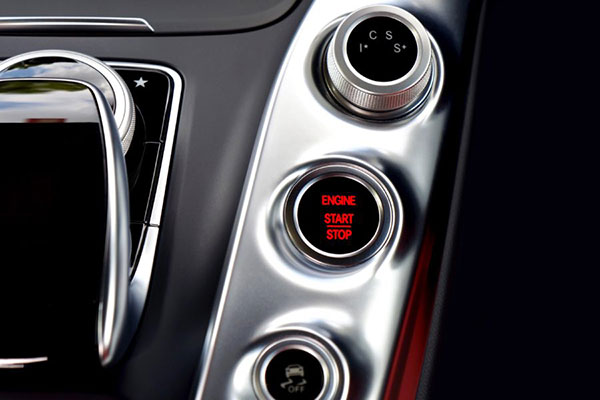
injection molding for automotive applications*
Durability
Let’s take for example commercial and residential buildings, its canals are mostly made of metals that rust and leaks with time. The installation is quite secure, but as time goes, they are susceptible to leaking from being in contact with water and moisture.
In modern apartment complexes, the canals are lined with PVC’s which will neither degrade nor damage for years to come. Well, the same principle also applies to mechanical components and parts boosting the longevity and lifespan of the mechanical components.
Improved and enhanced features
The rising use of plastics has everything to do with enhancing the overall features and components of your device. This will only start when you incorporate plastics into the production process, for most polymers used by manufacturers they come with a higher degree of dimensional stability as well as the reduction of noise emitted.
The precise and exact mixture of these compounds makes the polymer more durable and less dense. The risk of getting shocked is also significantly reduced, another vital benefit is the parts and devices can withstand high temperatures
Plastic injection molding will create components and parts that will be protected from chemical and environmental factors. Another essential fact that we can’t fail to mention is that plastics are quite cheap. This fact only will considerably reduce the cost of the overall production process.
Plastic injection molding is slowly becoming one of the go-to manufacturing technique, it comes with positives that outweigh the negatives.
Reference
*Image from https://www.rapiddirect.com/