Die casting is amongst the hottest manufacturing techniques at the moment as it allows you to manufactured parts and products with intricate and complex design while also at the same time the overall process being cost-effective and economical.
But if you are a newcomer in the die casting process, you might find the overall experience quite difficult, but once you get the hang of it; it’s quite simple and straightforward. If you are new to the die casting process, then this is the best place to be as we are going to show you how you can efficiently apply the design tactics for optimal manufacturability.
Design for manufacturability
Optimizing your overall design to take full advantage of the die casting process is vital if you want to recoup all your investments. Whether your project is designed for injected metal assembly, multi-slide die casting, or conventional die casting, it’s always vital to design your part or product with the production or manufacturing process in mind.
In simple terms, both designers and engineers should approach every project with the intention of design for manufacturability. DFM is a core methodology that ensures that all of the die-casted parts perform as expected which reduces the requirement for secondary options.
In simple words DFM is just a concept, it’s a way to cut down on all the efficiencies and reduce cost before your project goes into full production.
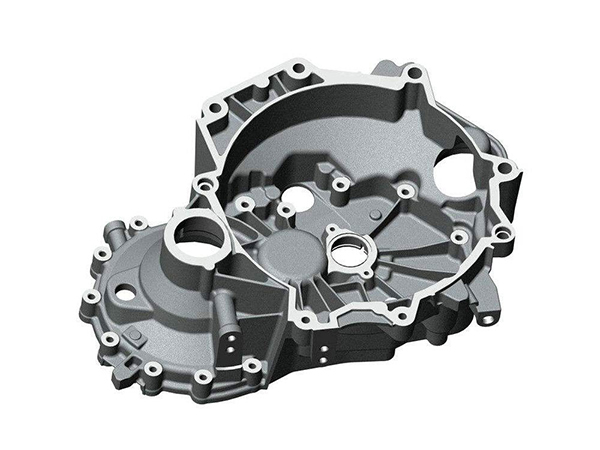
precision die casting products*
Reduction of wall thickness and weight
In die casting, two things drive the price and cost very high: machine time and materials. For those who want to reduce the overall cost, they can do so by thinning the walls and the addition of weight-saving pockets.
Reduction of the wall thickness and weight of the cross-section is the obvious solution, reduced weight means less material used which in turn means reduced material cost. What this also means the solidification time will be significantly reduced, thus enabling you to get more shots per minute. But, never sacrifice performance for cost.
Maintaining consistent wall thickness
Reducing the wall thickness is vital but maintaining the uniformity of wall thickness is key. This will be vital in ensuring repeatable and consistent casting that’s optimized for manufacturing. Non-uniformity of wall thickness is more than likely to result in porosity and weaker parts which will be very bad for your overall production project.
Working smarter and not harder
Modifying the design of your parts and product as well as tweaking the overall design before the final phase will not only enable you to fully take advantage of the die casting process but also align the whole process with your business needs.
As a novice or beginner, the die casting process shouldn’t be an uphill battle; but that should not be the case. In this article, we have covered some of the basics that you should always have at the back of your mind to have an easier time with your die casting process.
Reference
*Image from https://www.dumold.com/