Sheet metals are used in many applications like automotive and aerospace industries. It should be processed in a certain method in order to obtain the sheet metal. The source of sheet metals includes aluminum, stainless steel, zinc, magnesium, and other metals. Sheet metal manufacturing process includes four different techniques and can be known through this article. Sheet metals are very important in construction works, medical types of equipment, automobile and aerospace machines. The use of sheet metal made many new innovative technologies in different fields.
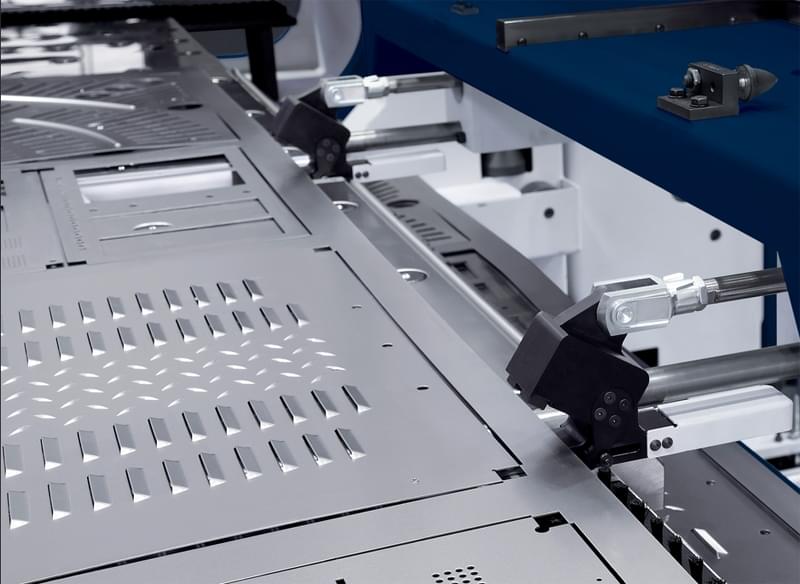
sheet metal*
Sheet metal manufacturing types
The sheet metal can be fabricated in four steps basically. All the four processes have been mentioned below.
- Bending metal:
This process involves two steps like
- Form bending: It is done by bending the metal directly with a hammer or over an edge.
- Metal brake: In order to get the metal in precise shape, metal braking method is used. For this process, the metal is placed on the flat surface where a flat bar gets clamped on the metal top. It helps in bending the metal to the desired angle.
- Cutting metal:
This can be carried out by the following processes
- Power shears:It is great in cutting the metal easily and quickly. It is available in many forms like pneumatic and electric shears. But the only disadvantage in this is it cannot cut tight corners or shapes that are very complex.
- Hand shears:They are used manually in metal cutting. It is the most important too that is available in every arsenal.
- Angle grinders: It is an electric angle grinder is a manual tool that spins with a disc or wheel attached to it. This disc-shaped thing helps to cut the metal easily. This is the most common type used in sheet metal manufacturing
- Throatless shears: These are designed to cut the metals with accurate radius. They are very useful in cutting metals without spoiling its edges. They are operated by means of the hand and they do not waste any material.
- Plasma cutters: It can cut the metal with a higher range of accuracy with a perfect finish. It requires only a little cleaning and is perfect for long sheets.
- Shrinking metal:
Shrinking the metal can be done by tucking, normal shrinking, or heat shrinking.
- Tucking:It is the earliest and ancient method of sheet metal manufacturing. This method involves tucking of the metal by using a hammer with the hands.
- Shrinker: This tool makes use of hands or legs for holding the lever. The lever consists of a moving and texture jaws that move the metal from top to bottom that forces it to be together. It gives a perfect finish than tucking metal type and also prevents from spoiling edges.
- Heat shrinking: Sheet metal manufacturers use heat at an area that is stretched by means of a torch. This gets shrink when allowed to cool.
- Stretching metal:
Metal stretching can be carried out by following processes like hammer and dolly, stretcher and English wheel.
- Hammer and Dolly:it is a stretching metal by holding an object behind metal and the opposite side is hit with the help of a hammer. This ultimately makes the metal to stretch by increasing the surface area. The similar method can be carried out for stretching metal by a sandbag and plastic mallets.
- Stretcher:It is exactly opposite to that of a Shrinker that helps in stretching the metal with the help of a lever held in hand.
- English wheel:It is also a stretching metal process in sheet metal manufacturing but has the ability to create curves. The metal to be manufactured is placed between a wheel which is faced up and a small radius anvil wheel. The English wheel makes the sheet free from imperfections.
Applications of sheet metal manufacturing
- Automotive industry: It is used in the modification of your car for changing the existing radio or for building a new sound system.
- Medical field: Sheet Metal manufacturing helps in the field of medicine for making customized beds for hospitals, physical therapy equipment, sterilization cases, blood sort systems by robots, and in branches like cardiology, neurology, ophthalmology.
- Aerospace applications: Various tools are used in aerospace industries like harness components, aircraft body, bezels types, EMI assemblies, RFI assemblies, chassis components, optical sensors, and other structural components.
- Oil and gas industries: Sheet metal manufacturing helps in oil and gas industries by providing equipment like adapter plates, specialized pipes, and metal louvers, storage tanks for extraction and processing, heavy-duty dampers, butterfly dampers and so on.
- Construction industry: Sheet metals are used in construction industry for making stainless steel fountains, sculptures, aluminum enclosures, metal concrete bodies, automatic gates in metal, floor tread plates, designed floor and ceiling patterns, and so on.
Sheet metal manufacturing is a very much useful technology in many fields. It is the process that can bend, cut, shrink, and expand. This malleable and ductile property of the sheet metal helps in manufacturing many tools and equipment. Also, these sheets can be made into different shapes and forms. There are also other types of sheet metal manufacturing processes like laser beam cutting, water cut jetting, plasma cutting, deep drawing, and punching. It is used for cheap and affordable furniture and other consumer products.
Reference
*Image from on https://www.minifaber.com/