A manufacturing workshop offering vacuum casting services to bring a prototype to life it’s not a novelty, but it shows a high level of experience from the company. It turns out that vacuum casting is probably one of the most effective methods to create incredible prototypes for end-use products that need low production runs. Most of the details are ironed during the planning stage, but when we strip it down to the basics, we end up working with pourable resins to create casts and silicone molds that have a high rate of re-usability to generate series of well-crafted products using a master pattern.
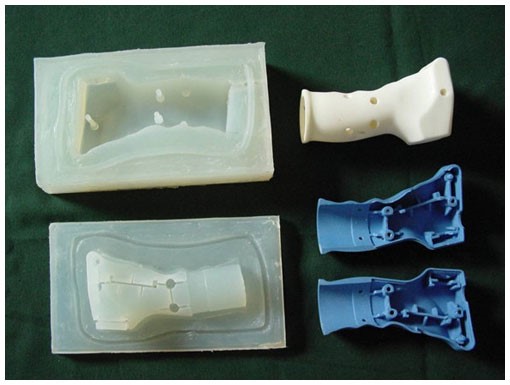
vacuum casting products*
Prototypes created using vacuum casting services are some of the most useful test models you can have. They can be used to tests the performance of the engineering of the part. They are also helpful for diverse stages of product development. These prototypes are also visually rich so they can be used as display models for marketing purposes or crowdfunding of your ideas. Vacuum casting is also one of the most flexible means to create anything from scratch. It’s cheaper than most prototype procedures because it works better with plastic resins. This is often considered as a limitation by some, but in the niche of vacuum casted products, it reigns supreme.
Here are some of the most important advantages to vacuum casting services:
You Get to be Creative with Your Master Pattern
Vacuum casting begins with the planning and creation of a master pattern. This is essentially a first-stage prototype created using durable resins. Most master patterns are created using 3D printing or CNC machines, but these methods are favored for larger production runs and faster output of larger orders. They also don’t require the level of tooling that goes into vacuum casting. A master pattern needs a bit more craftsmanship before a mold can be created out of it. Sanding, polishing, and painting are required to make the product look right. Assembled parts require additional detail as well as test assembly to make sure everything fits in place.
Making the Mold Signals your Output
We have already made a point about the level of detail that goes into the master pattern. Once that stage is done, the pattern will have to be cast in a special box. The process is somewhat stressful because silicone must be poured on it at a certain pace to make sure it covers all the corners and fillings of the master pattern. The curation of this mold it’s probably the most essential part of the process since we need the silicone plastic to harden properly. Once this stage is done, we’ll get an imprint of the original down to the last detail. The mold is essentially a cutout of your product, and you will use it to create as many reproductions as you need.
Resin Quality Determines the Success of the Mold
We already know that vacuum casting works by pouring resins inside the mold we created out of our master pattern. While it’s true that this manufacturing procedure it’s only for short production runs, it’s the quality of the resin the one that will determine the durability of the mold. The average figure for a vacuum casting mold is about ten to twenty parts. But the output can be a tad larger if you use quality resins for the master pattern with lesser versions for the finished part. Vacuum molding services are great to create limited runs of products for a niche market. If you wish to learn more about this, visit us at LTC Proto!