Plastic molding makes plastic parts and products. Molten plastic is poured into a mold and cooled to make the desired shape. Plastic molding is popular for manufacturers because of its benefits. We’ll discuss why plastic molding is useful for manufacturers.
Versatility
Molding plastic can take on many forms. The method yields plastic components of varying dimensions and configurations. The procedure can be modified by the manufacturer to produce pieces with a wide variety of contours, dimensions, and surface finishes. Molding plastic is used to produce automotive components like bumpers and dashboards. The procedure results in intricate parts that have a high degree of precision as well as tight tolerances for smooth fitment. In the field of medicine, it is utilised in the production of medical implements such as syringes, inhalers, and catheters. This method results in parts that are accurate and sterile, which satisfies the requirements of the industry.
Cost-Effective
Plastic injection molding is an economical option. Machines and efficient procedures cut down on the cost of labour and enhance output, resulting in cheaper individual components. When you use parts of a higher quality, you need to do less finishing and assembly, which saves money. Molding plastic is used in the production of consumer items. Toys, cookware, and other small appliances are included in this category. It is an economical method for producing huge volumes of parts that are durable.
Efficient and precise
Plastic molding makes plastic parts fast and accurately in large quantities. CAD and CAM software make molding precise and consistent. Aerospace industry uses plastic molding for aeroplane parts. The process creates precise, lightweight, and aerodynamic parts that meet industry safety standards.
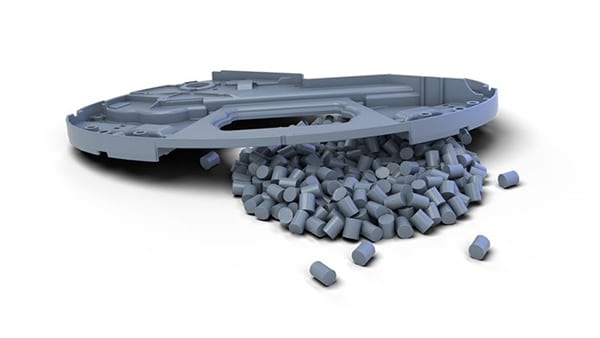
plastic parts*
Durability
Plastic molding is durable. This process creates durable parts and products that can withstand wear, impact, and harsh environments. Plastic molding is great for durable products that will be used a lot or exposed to the elements. Construction uses plastic molding for making pipes, fittings, and insulation. The process makes strong parts that can handle moisture, high temperatures, and other environmental factors.
Customization
Molding things out of plastic also provides opportunities for personalization. It is possible for manufacturers to make components and finished goods that are individualised to fulfil the specific requirements of their clientele. This makes it possible for manufacturers to separate themselves from their rivals and offer distinctive products that are tailored to the requirements of their target market.
For instance, the electronics industry makes use of plastic molding to produce parts like computer keyboards, cell phone casings, and other electronic components. This technique is also used to generate different types of electrical components. The technology makes it possible to produce components that may be tailored to the requirements of particular devices and the specific preferences of individual customers.
Molding products out of plastic is a useful technique for manufacturers because it has a number of advantages, including as adaptability, low production costs, high levels of efficiency and precision, long-term durability, and the capacity to be customised. Plastic molding gives manufacturers the ability to produce components and goods of superior quality and consistency, which not only satisfies the requirements of their clientele but also enables them to maintain their position as market leaders in their respective industries.
Reference
*Image from https://www.gom.com/