Vacuum Casting is known by different names such as Urethane casting and Polyurethane casting. This process comprises silicon molds that help to make different components from rubber and plastic under a vacuum. This process mimics the injection molding to produce various parts of polyurethane and cast nylon.
As the process takes place under vacuum conditions so there are no chances of air bubbles and the products are of high quality and bubble-free. This process is also used to get a smooth surface texture without any flaws.
Vacuum casting is helpful in rapid prototyping and it becomes more useful when it comes to producing rubber and plastic parts.
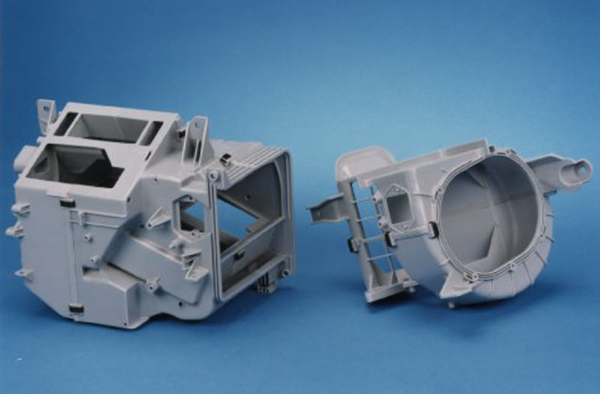
vacuum casting products*
Characteristics of Vacuum Casting:
- It is the most effective method to manufacture low-volume plastic components with high quality. These may be similar to the injection molding parts.
- Different materials can be used in this process to produce translucent, opaque, and transparent parts.
- Different vacuum casting resins are available to create different parts that satisfy different requirements including temperature, surface textures, and toughness of the product.
- Great quality wax masters are also made through vacuum casting because it enhances the features and finer details of the product.
- Vacuum casting is suitable for fit, form, and functioning tests of the products.
Technical Specifications of Vacuum Casting:
Standard lead time: 30 to 50 parts can be produced within 4 working days using this method.
Material choices: You have different material options. So you can test different materials to get the best one for your project.
Standard accuracy: The standard accuracy of vacuum casting is 0.3%. The lower limit is 0.3 millimeters for dimensions that are smaller than 100mm.
Minimum wall thickness: The 0.75-millimeter thickness of the wall is important to make sure that the mold is properly filled. To get better results 1.55-millimeter thickness is recommended.
Maximum part dimensions: The size is limited by the vacuum chamber’s dimensions.
Surface structures: Matt surface or gloss surface can be obtained by this vacuum casting.
Advantages of Vacuum Casting:
- Vacuum casting is used to produce small numbers of injection molding-type parts. It will reduce the time for cutting stage and cost to develop new products.
- Different casting resins are used for different applications such as rubbery, flame retardant, clear and food-grade.
- Complex shapes can also be produced by using multi-segmented cores and molds.
- Bras and aluminum in-mold inserts are also used.
Disadvantages of Vacuum Casting:
- As the molds are manufactured withsoft silicones. It is manufactured quickly and can be used for about 50 parts only. Tool wear depends on the size, feature, and surface textures. Rough surface textures and big parts reduce the mold life.
- The sharp corners of the part may become rounded sometimes.
- Due to flexible mold and thermal expansion of the liquid the shrinkage rate is increased to 15%.
- Likewise,with rapid tooling or injection molding, more thin and thick or irregular features may diverge from the normal tolerance.
- To get additional features in the products, you may need cores and plugs.
Reference
*Image from https://www.scott-am.com/