In case you’re wondering what the cheapest method for creating a prototype is. You might want to look into vacuum casting. Vacuum casting calls for curing materials at precisely the right temperatures.
Shrinkage can be kept to a minimum by maintaining a vacuum pressure for five minutes at a molding temperature of sixty degrees Celsius and keeping the resin at thirty degrees Celsius.
Duplicating something with a silicon mold is similar to vacuum casting. The process of plastic vacuum casting with silicon molds was pioneered in German institutions in the 1960s.
Why did you decide to use vacuum casting for your business? Here, you’ll learn more about that if you read on.
Vacuum Casting
Casting elastomers requires a vacuum to pull any fluid material into the mold, where it solidifies. Whenever air trapping is an issue with the mold, the process is switched to vacuum casting.
As a bonus, the method can be employed even if the mold features complex undercuts and other fine details. When the mold is made from fiber or expanded wire, this technique is also used.
Due to the rapid prototype stage of production, where the panels are heated, the method is sometimes referred to as thermoforming. Computerized vacuum casting equipment is used to warm the ingredients until they are malleable.
How does it Work?
A procedure is employed to create the end product with vacuum casting.
1. Master and superior model
Having an excellent master model is essential for the vacuum casting process. The superior prototype itself can serve as the functional prototype for the manufacturing component. In the realm of prototyping, you may also make use of a model made with stereolithography.
When using a master model, check that it has the right proportions and aesthetic appeal. Taking these precautions will guarantee that the final prototype model is free of any defects introduced during development.
2. Process of Medicative
Next, a silicone adhesive mold of two parts is made using the master model as its pattern. High temperatures are used to cure the mold, guaranteeing that the components will stay attached. The mold will be sturdier and more long-lasting after this has been applied.
When the mold has hardened, it may be sliced open to expose a cavity that is the precise size of the master. The vacuum chamber is where the mold goes after it has been split in half. Later, the specified material is poured into the mold to complete the product.
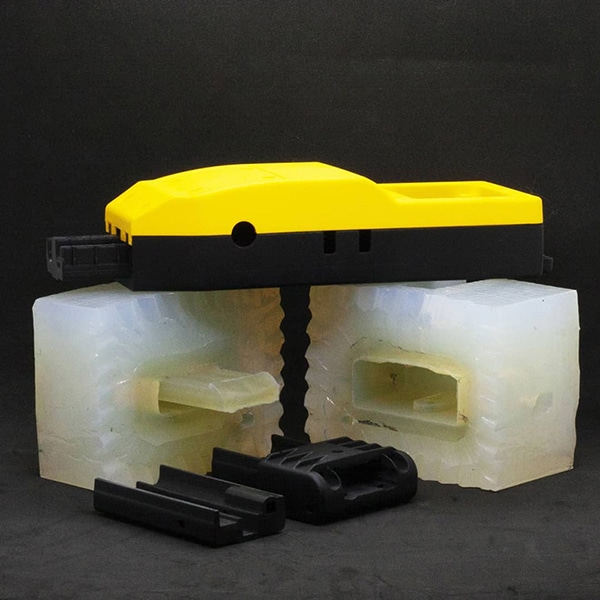
vacuum casting products*
3.Resin Filling
The specified material should be used to fill the mold. The properties of industrial materials are mirrored in the resin. When resin is used for aesthetic or utilitarian purposes, it is often combined with powder particles or other colored pigment.
When the mold has been loaded with resin, it is taken to a vacuum room to cure. To eliminate the possibility of air bubbles, the mold is put into a vacuum chamber. So that nothing goes wrong with the final output, this must be done.
4. Lastly, curing
For the last step of curing, the resin is heated in an oven. Extreme heat is used to cure the mold, making the final product tough and long-lasting. To reuse it for future prototypes, the silicone molding is disassembled.
The prototype is painted and embellished after being released from the mold. Stunning visuals are achieved through the use of art and design.
Conclusion
In comparison to 3D printing and injection molding, the cost of vacuum casting is significantly lower. You can increase output while decreasing expenses in this way. If you want to learn further about the casting process and silicone casts made using this cutting-edge technique, go here.