CNC machining is a highly efficient technique. All of the essential procedures are automated using cutting-edge technology, making the process quick. To guarantee that the findings are correct, the remote sensing industry demands high-quality goods.
In the industrial business, CNC machines are designed for maximum productivity and performance. Customizing components for use in remote sensing instruments guarantee high-quality output. Without any mistakes, the basic materials are converted into the correct forms and sizes. Here is some vital information about CNC machining services.
The high degree of accuracy
To acquire data, all remote sensing instruments employ laser beams and sensors. These devices are essential in places that are physically difficult to access. As a result, for appropriate decision-making, the data must be accurate.
For the sensors to be helpful, they must have a high level of accuracy. CNC machining uses pre-programmed technology to create identical components with high degrees of precision.
Scientists, researchers, and intelligence professionals benefit from weather satellites, aerial photography, and light detection tools. There is no space for error when designing these parts utilizing CNC machining. It also creates one-of-a-kind items that are customized to a particular sensory instrument. In the aerospace sector, this production process is critical.
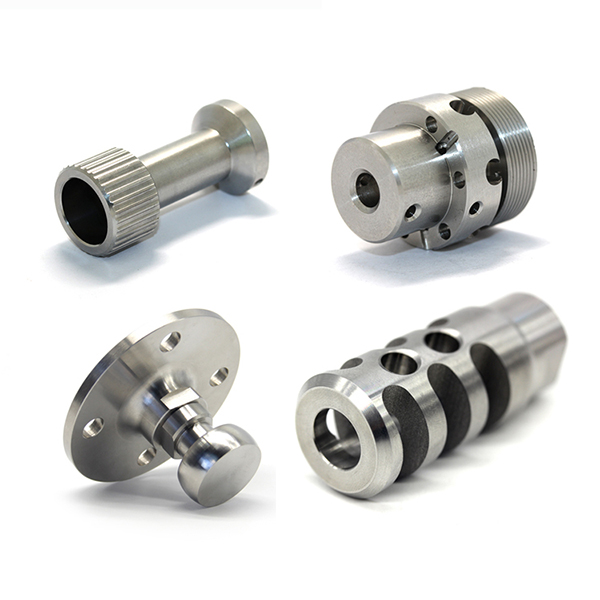
precision cnc machining parts*
Developing prototypes
Prototypes are required in any business before mass manufacturing can begin. Players in the aerospace sector can employ the services of a CNC machining firm to manufacture draught versions of new parts for use in remote sensing instruments.
When gathering spatial data, these prototypes can be used in feasibility testing and evaluations. Because the Earth’s environment is constantly changing, scientists or military people can use a prototype to test the instruments and see if they operate correctly.
These tiny pieces are ideal, especially if any improvements or adjustments to the materials used in customization are required. The industry of remote sensing is likewise vulnerable. As a result, firms working in this field may use the prototype to patent their products and ideas, ensuring that they are protected from rivals.
Convenience of manufacture
With each manufacturing, CNC machining creates precise and particular pieces. The programming of CNC machines and software guarantees that all of the parts are consistent. To provide reliable findings, remote sensing tools rely on the same technology each time.
Manufacturers of CNC components can fabricate exact replicas of features and tools found in a certain radiometer. These procedures use automation and high-level technology to produce outputs that match customer requirements.
Longevity of tools
Custom CNC components are incredibly long-lasting. In contrast to other produced components, their material composition is unrivaled. They are exposed to various air conditions, including extreme temperatures while doing remote sensing operations. Because of their increased strength, they will keep their form.
When this technique is used to manufacture remote sensing instruments, the cost of replacing parts is considerably reduced. Clients may also use the tools to increase their productivity and production during data collecting and reporting for a more extended period.
Material alternatives
Different materials are used to create various geospatial technology tools. Whether the pieces are made of plastic, wood, ceramic, rubber, or metal, CNC machining can get the job done.
The manufacturing company’s product teams can aid in the selection of materials for a given product. Based on how they use the sensory instrument, they can estimate the resistance needed, the materials required for each section, and how much it will cost. CNC manufacturers can help you save money by advising you on the best materials to use.
Reference
*Image from https://www.cncmachingparts.com/