One of the most simple and basic definitions of rapid tooling is the creation of molding cast within the shortest time possible, the science behind this project was developed back in the 1990s. The tooling technique came about as engineers were looking for ways on how to optimize all the tooling procedures within a short time frame, as the conventional method took months.
The scientist came up with news ways of creating patterns within a few days in the final stages of mold creation, rapid tooling is one of the go-to techniques that create inserts on a finished product like the cavities and cores. Most rapid tooling molds can be used now to craft thousands of parts as well.
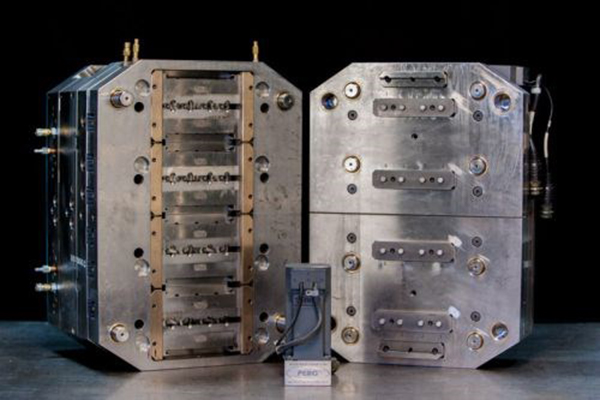
rapid tooling machines*
Things that you need to know about rapid tooling before getting started
Modern technology has created various types of rapid tooling. Every type of tooling technique comes with unique benefits based on the materials that you’ll use. Most of these manufacturing techniques will provide better practicality depending on the technology being used.
The level of precision and accuracy is very vital as well as consistency. It’s vital worth noting that rapid tooling also comes with certain limitations in place, so it’s important to keep these observations:
- The mold used must be sturdy and strong enough to handle all the injection molding processes, the devices use will measure and gauge strength by the pound per square inch. They will also clamp the two parts attached to the mold creating a perfect product. The molds must be able to with stand high temperatures as most of the time they will be handled in a molten state. If your mold has limited longevity, then they will not last for a long time.
- Another vital aspect is that the mold will have to have a smooth surface finishing on the inside, every part of the product and prototype must be created and ejected with minimal problems and a clean and smooth surface. To attain this, most manufacturers are known to put in extra work on the mold together with extra phases of development.
- The last thing that will deal with is the tolerances of the mold. A lot of mold being currently used don’t have tight tolerances, and they’ll require additional adjustments. For those developing plastic injection molded products, the mold must have a tolerance of +1,001 to avoid leaks. Leaked materials are one of the first sources of material wastage that will affect the integrity and output of your mold.
Rapid tooling is amongst the few available techniques that will create just about any product, the demand for quick turnaround time is always on the rise as clients get ever-more specific and demanding; rapid tooling will enable you to achieve all your objectives as well as meet your client’s needs and specifications.
Even though there are a few limitations, the good outweighs the bad and as a manufacturer or client, you shouldn’t hesitate to incorporate this technique into your manufacturing procedure.
Reference
*Image from https://www.ptonline.com/