Most of the items we are using every day are products of injection molding. Have you ever wondered why this is so? The reason is simple. Injection molding is an extremely versatile process in producing parts and products. It is the most preferred method because it offers multiple advantages.
In this article, we are going to look into the reasons behind its popularity. Let us take a deep dive into the world of the plastic injection molding process.
What is Plastic Injection Molding?
The plastic injection process is one of the most common techniques in producing large quantities of plastic products. Some of the most common everyday things that are produced by plastic injection molding include toys, disposable cutleries, chairs, consumer electronics casing, and many others.
The injection molding machine has three major parts: the plastic injection, clamp, and the injection unit. There is a separate unit to contain the material which heats the plastic pellets. Upon melting, this material is pushed forward and injected into the mold cavity where it will take shape. Once the material is cured, it will form the plastic part. This part is then ejected out of the mold, and you’ll have the final product.
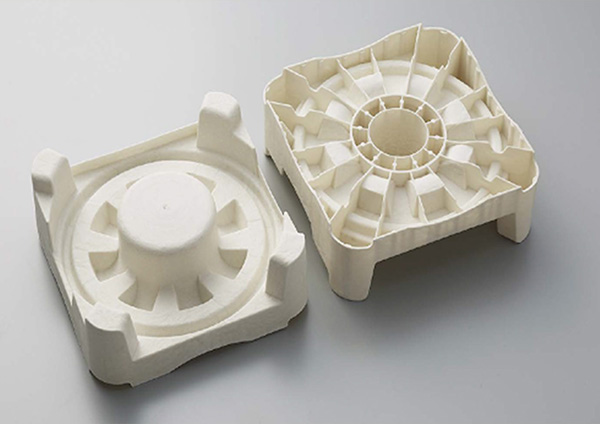
Pulp injection molding products*
Why is Injection Molding Popular?
Manufacturers are looking for a process that can make their products at the lowest cost, and injection molding service is the right answer. The automated nature of this process requires only machines and robots with a single staff minding the whole process.
Automation helps reduce the manufacturing costs, and the overhead is significantly reduced. When you have a reduced overhead cost, that means the cost savings is passed into the customer. Furthermore, injection molding has high repeatability and low scraps, which contributes further to its reduced costs.
Another reason is the ability of the injection process to make products with complex geometry and complex features. Since the injection molds are subjected to high pressure, the material is pressed harder against the mold, which other manufacturing techniques cannot do. As such, it can accommodate large details of the design. The same high pressure in the molding process is also the reason why you can incorporate intricate and complex designs into its products.
Another quality that manufacturers are looking for is high efficiency. With injection molding, the process is very quick. Once the injection molds are prepared according to the specifications of the customers and the process is programmed, the production run will commence quickly. It has a high production output rate, which makes the process more efficient and cost-effective.
The products from injection molding are strong because it is possible to use fillers in the injection molds. It contributes to the reduction of density on the plastic while being molded. Plastic injection molding can also use different types of materials at the same time using co-injection molding.
The last reason why the injection molding process is the go-to production technique is due to its ability to produce the same products and masse. With injection molding, you can conveniently achieve economies of scale. The cost of production is less, and with its faster cooling rate, machining and finishing can be done faster, and the lead time to market is cut short.
Reference
*Image from https://nisshausa.com/