The manufacturing world is very competitive and time is always valuable. This applies to all the techniques in producing a part including CNC machining. It could improve the machine’s efficiency if you could save time before and after machining.
Why should you care about saving time on CNC machining? The answer is simple. With today’s advancement in CNC machines, you have to optimize its productivity and process as much work as you can. Here are some tips on how you can optimize your CNC machining process.
Tips to Maximize Your CNC Machines
1. Adopt Lean Manufacturing Method
To maximize the process, you need to go down the macro level and that means adopting lean manufacturing practices to minimize waste. The very principle of lean manufacturing is optimization. It is not about working faster as it can lead to errors. It means improving the process and creating quality parts faster than how you normally do.
One way to optimize the process is by updating the machine. Technology plays a great role today and machines are evolving. You should look into upgrading your cutting tools, tooling, and other components like sensors to provide real-time data for reporting and analysis.
2. Get Into Optimization Mindset
It may sound easy when you hear it but there is plenty of work to do to get the team into the optimization mindset. What manufacturers needed to do is to organize a game plan, simplify tasks, and train their personnel.
A clean work area for your CNC machining will have all the tools and components within reach. Simplification, on the other hand, is doing extra to minimize computations for tolerances and having all the information on hand. These steps will save time and limit frustration.
3. Push the Machine and Its Tooling to the Maximum
Since CNC machines are designed to go fast, why not maximize their capability? Ensure that the machine is not idle because it will go to the overhead. If possible, keep it busy all the time. Optimize its built-for-speed feature to achieve its performance level.
The operators should understand the unique set of machines and their capabilities. Put them in targeted training to identify the areas where they struggle and enhance their competency in handling the process. The better they are at the job, the faster and safer it is to produce the part.
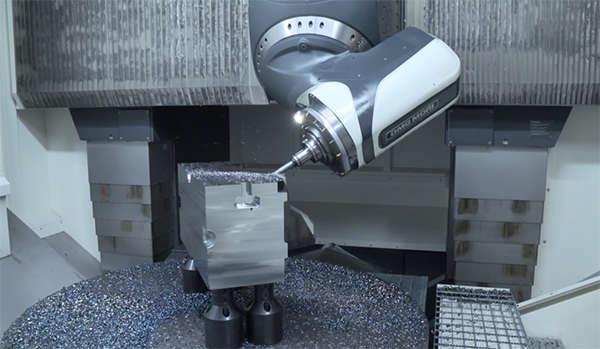
5-axis cnc milling machines*
4. Keep Track of the Cycle Time
Manufacturers can calculate cycle time by dividing the machining time by the number of parts. The results, however, are not precise information. By automating the data collection with each CNC machine. This way you can get accurate information. You can have greater efficiency if you focus on saving time at the machine level.
Another thing to take advantage of in the machine is its 5-axis. If you can use the same tools for different cuts, you are cutting (pun intended) the cycle time. You are saving time on tool changeover and get more efficiency.
Reference
*Image from https://www.autodesk.com/