You can see products from injection molding everywhere. From children’s toys like Lego blocks to the turbine blades of a space shuttle, it is evident that plastic injection molding plays a vital role in our daily lives.
There is no denying that this manufacturing process is the most popular among the techniques available. In this article, we are going to discuss the essential facts that you need to know about plastic injection molding. It will give you an idea if it is the right manufacturing process for you.
Injection Molding Defined
Injection molding is a common manufacturing process used in producing large quantities of products made from glass, metal, plastic, or rubber. It is a straightforward process. So simple that it resembles the same process in making Jello. It involves injecting the molten materials into the mold and letting it settle into a solid-state.
Plastic injection molding uses a molten plastic material to create plastic parts. It is one of the oldest manufacturing processes. The process originated in 1872 when an inventor named John Wesley Hyatt gained the patent for the first plastic injection molding machine. It was invented to replace the ivory balls in billiards with plastic balls. The balls were not successful, but the machine was.
Since its inception, the plastic injection molding technique is most progressive. It rapidly evolves from producing small parts to the most complicated products like medical equipment.
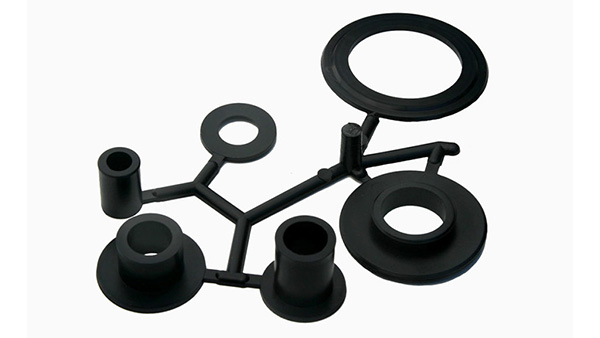
Injection molding parts*
Applications of Injection Molding
The products made by injection molding have plenty of applications. Manufacturers use it for high-volume production. It is used to make large objects like garbage cans to small objects, like cases for mobile phones.
The most common application of plastic injection molding is for making non-consumer parts where there is no demand for aesthetics like the mechanical parts of a bigger object. It is because the injection molding process often has imperfections and impurities on the plastic parts.
Benefits of Using Injection Molding
Plastic injection molding is one of the fastest-growing manufacturing industries. It has seen its rapid expansion in the 1980s and even today, it has outpaced the many other techniques. Here are the reasons why it is preferred by manufacturers.
- Mass Production – Plastic injection molding is the fastest manufacturing process, hence it perfectly fits the demand for high volume production.
- Low Wastage – Unlike in subtractive manufacturing like CNC machining, where the machine cuts away a large part of the block to create the item, injection molding has less wastage. It is more efficient and uses an exact amount of material to create the product.
- Complex Parts – Plastic injection molding can create intricate complex parts. It can cut down the number of separate parts to make one object, which further cuts down the overall production time. It also eliminates secondary operations and allows you to mold your design and brand into the part.
- Low Production Cost – Because plastic injection molding has less wastage, it is also a less expensive process. The material is also less expensive compared to rubber and metal. Another cost-saving feature of plastic injection molding is it’s recyclable. The by-product can be “re-grind” and used again. The initial cost of investment is also cheaper than other production techniques.
- Consistent Quality – The injection molding process is highly repeatable. It can produce thousands of parts with the same quality. It also has a lower rate of rejection.
Conclusion
Injection molding is the best manufacturing process for producing a high quantity of parts. It is a popular technique because it can make identical plastic parts with good tolerances.
Reference
*Image from https://rexplastics.com/