When choosing a manufacturing process for your project, you may have questions that you want answers before letting it push through. On top of your list would be the factors that could impact the cost of your project and how you can use your budget efficiently.
Did you know that you have the answer right there? To answer the second question, you have to know the factors that would affect the cost of your plastic injection molding, which is the first question. Your finance guy calls them cost drivers. And when you are aware of these cost drivers, you can develop the product with the specifications in mind.
Knowledge of these cost drivers will also be in your arsenal when discussing the manufacturing options with the plastic injection molding company.
In this article, we will enumerate the cost drivers that affect the unit cost of plastic injected parts.
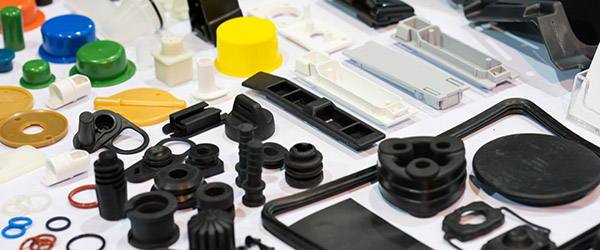
plastic injection molding parts*
Part Design
We are not talking about the design of the part that serves its purpose here. The design we are talking about is in the cost sense. In terms of cost, a design that meets the specs as efficiently as possible is the best design.
From the beginning, designers of plastic parts are looking at how to reduce the cost on the upfront and overtime cost of production.
For the upfront cost, the designer has to consider the end-use, materials, logistics, budget, production volume, tooling, and the cost of running the production. Designers who are not addressing these considerations will allow cost to balloon.
Other than these, some costs would come up during the process including high reject rates, not meeting the timeline, and extra labor. All these are due to poorly designed parts.
They should also consider the cost of packaging and transport of the parts. A well-designed part also considers the space needed to store and ship the finished part.
Tooling
No plastic injection molding can run without the tool placed on the injection molding press for the plastic material to take shape. Most of the tools are custom-made, and their costs will depend on the design of the part.
For large parts, you will need a large tool, and that means it would cost more. However, each part made from this tool will share the investment. If you have a complex design, the tool is also complex.
In tooling, you get what you pay for. If you acquire cheap molds, you should be prepared for more maintenance. It will also break faster. A quality tool may cost more upfront, but it has no repair cost and will not hamper production.
Cost of Each Part
Unit costs are how much is the individual part you make. Ideally, the unit cost is something you know at the beginning of the plastic injection molding process. But that is not the case. To achieve the most efficient production run cost-wise, designers need to balance three things: material, cycle time, and labor.
Material is the resin used in each part, and the lesser material used the better. However, the part should meet the design and the customer’s expectations.
Cycle time, on the other hand, is how long will it take to make the part. This is determined primarily by the size and shape of the part.
Labor refers to how much time an operator has to spend to make the part. Some parts are ready as soon as it comes out of the injection molding machine. Others need cleaning up and finishing.
Conclusion
In the plastic injection molding process, you need to consider these three cost drivers to get a good return on your investment. You should ask for good part design, acquire quality tooling and focus on bringing down the unit cost to make high-quality parts.
Reference
*Image from https://www.fordatlantic.com/