The vacuum process is an advanced and economical way to create prototypes. All it needs is the right optimum temperature to cure the materials. It is the manufacturing technique to use with small volume requirements for functional testing or prototyping. It is a two-part process that uses polyurethane and silicone molds.
Vacuum casting is a flexible and dependable process that can accommodate complex geometries. Aside from prototyping, most companies use vacuum casting as a bridge before going into full production. In producing the part, the first step is to have a high-quality master prototypical pattern.
The casting models are typically made through 3D printing, specifically stereolithographic. It can create models and patterns through a layer by layer process called photopolymerization. It is a critical part of the process because the master model has to be perfectly designed and made with high-quality. If not, it will only transfer the flaws to the finished products.
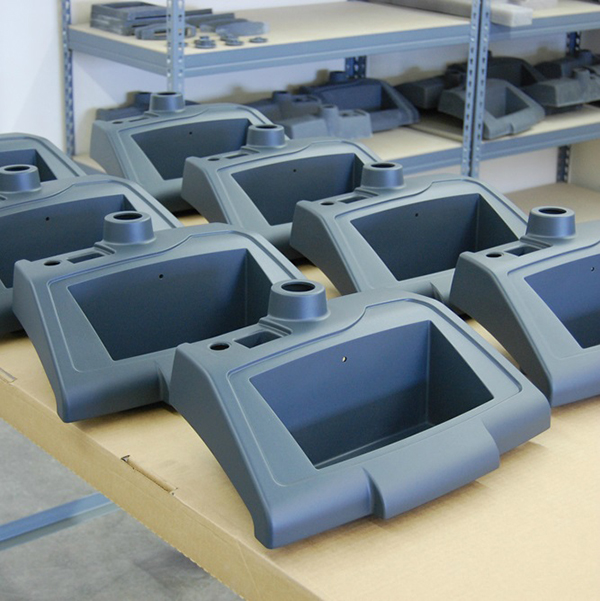
Vacuum casting molds*
The Vacuum Casting Process
As we have mentioned earlier, the first part of the vacuum casting process is the production of the master copy. Once you have the model, it is inserted into a two-part mold made of silicone. The mold is then subjected to a very high temperature, cured, then opened asymmetrically. The master model creates a cavity within the mold in its exact copy. This is now the final mold where the final product will be cast.
The difference of the vacuum casting method from other casting processes is that it is placed inside the vacuum chamber. While in the vacuum chamber, the mold is filled with the desired material. The most common material is urethane, hence the reason why vacuum casting is also called urethane casting. Urethane is perfect for vacuum casting because it mimics the needed characteristics of industrial-grade materials like polycarbonate, high-density polyethylene, and glass-filled nylon.
The vacuum chamber ensures that no air bubbles are trapped. Once the process is done, the mold is opened, and the part will undergo post-production steps.
Ways to Prevent Air Bubbles on Silicone Molds
The biggest challenge in vacuum casting is the air bubbles in the silicone mold, which renders it unusable. Here are the ways to have air-free silicone molds.
- Careful Pouring Methods – the surface where the casting material and the silicone mold meets is critical: it needs special care to avoid the formation of bubbles while the silicone is being poured into the mold. Pour the silicone in small quantities into the mold box and at an angle.
- Application of Compressed Air – Air compressor can pop out the air bubbles. Apply this after applying the first round of rubber to blow it over the model and wet its surface.
- Use Vacuum – The vacuum chamber can help remove the formation of air bubbles that are trapped during the mixing process.
- Use Pressure – The pressure on the material will help squeeze out the air bubbles formed on the surface of the mold.
Vacuum casting is an economical way to create functional prototypes compared with injection molding or 3D printing. It helps manufacturers to make more parts at a lower cost. Although it has its drawbacks, there are plenty of ways to overcome the challenges it poses.
Reference
*Image from https://purpleporcupine.com/