Wax casting is a technology used by artists all around the world to create several small minute sculptures. A wax model of an object is used to create a master mould. After the completion of that process, molten metal is poured to create the sculpture model. This technique has been in practice for more than 1000 years.
Vacuum casting is the process of making rubber or plastic models using silicone mould under a vacuum. It can produce complex parts exactly and cost-effectively in polyurethane resins. Being under extreme vacuum pressure it produces high-quality, cost-effective casting with smooth surface texture without bubbles. Widely used in rapid prototyping injection of moulding parts.
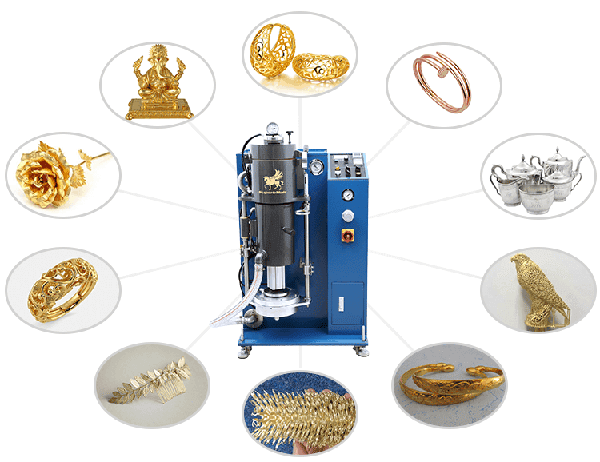
vacuum jewelry casting machine*
Unique features about vacuum casting & its applications:
- It is one of the most cost-effective ways of producing casings at high quality and low volume; Moreover, the plastic or rubber parts manufactured will be more similar to the injected ones.
- Parts produced from vacuum casting are more suitable for form, fit and function tests.
- The availability of more vacuum casting resins helps to satisfy a wide range of design requirements such as hardness, texture, rigidness, etc.
- High-quality wax masters can also be made using this type of vacuum casting to fit its requirements in investment casting.
Working Process of Vacuum Casting
This works similarly to the traditional injection moulding machine. It requires a mould tool made of metal, steel or aluminium with a similar part-shaped cavity to initiate the process. Soft silicone moulds used here make them more accurate and effective.
- 3D Design- In this modern world, every design and process starts with a 3D model. Similarly here in vacuum casting, 3D designs are made as per the moulding design guidelines to achieve better results. Sometimes designed parts are examined and tested for output by using laser scanning technology.
- Master Pattern– Based on the 3D model master pattern is created. Even though traditional methods of CNC machining are available making use of SLS technology can reduce cost and time. If the cast model is already there to use then we can skip this step. Make sure that the pattern is capable of withstanding 40℃.
- Silicon Rubber mould – Create a silicone rubber mould of the jewel. Then the master pattern is suspended inside the casting box. Silicone is poured around the vacuum to avoid bubbles and ridges. To avoid stickiness and surface defects proper scalpel has to be used while splitting the mould.
- Mix and pour exact proportions of resin inside the casting machine. Before the mixing stage, it has to be preheated at a required temperature.
- De-mould the cast part – Casting is removed from the mould and then allowed to go for any additional testing or quality checking process.
A wide variety of vacuum casting machines are available online, you can get your jewels customised by hiring any one of the vacuum casting professional companies available online. Dentists have been using these techniques towards creating dental parts. Not only in the medicine and art industry but also in the jewel-making companies that are making use of this wax casting process. It plays an effective and accurate role in making minute small pieces of jewellery.
Reference
*Image from https://www.superbmelt.com/