Traditional production methods make high-quality parts expensive and time-consuming. However, technology has enabled the creation of new production processes like vacuum casting, which offer exceptional surface detail, dimensional accuracy, cost-effectiveness, and sustainability.
It includes making a mould of an item, filling it with liquid material, then removing the air to harden it. A high-quality item with great surface detail and dimensional precision can be employed in automotive, aerospace, medical, and consumer products.
This article discusses vacuum casting, its applications, and its benefits. We will explore vacuum casting materials and their pros and cons. It can be a more sustainable and cost-effective manufacturing alternative for several sectors.
What is Vacuum Casting?
It produces high-quality polyurethane, silicone rubber and epoxy parts. A master template, produced from wood, plastic, or metal, starts the process. A silicone rubber or other mould is made around the master pattern.
A vacuum pump removes air from a vacuum chamber that holds the mould. Degassing prevents mould air bubbles. After degassing the mould, liquid material is poured in and sealed to maintain the vacuum.
The liquid material solidifies over several hours, depending on the material. After the material solidifies, the mould is withdrawn from the chamber and the part is taken from it. The part has great surface detail and dimensional correctness.
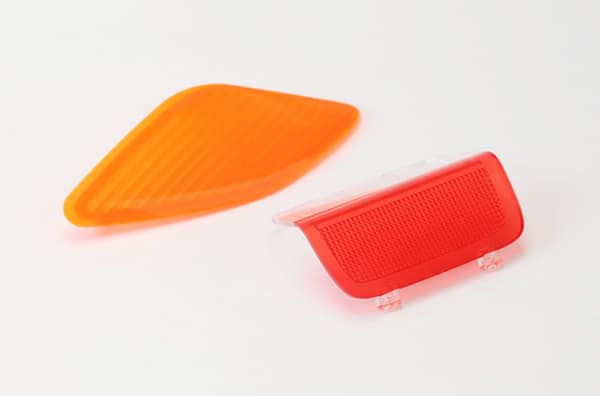
vacuum casting parts*
Its Applications:
Automotive, aerospace, medical, and consumer products use vacuum casting. It makes complicated items with detailed features possible.
It is used to make concept and pre-production car parts. Designers and engineers can verify part fit and function before investing in expensive tooling and production runs.
Satellites, rockets, and other spacecraft employ vacuum casting to make parts. The method produces lightweight, high-strength products that can resist space conditions.
It makes prostheses, orthotics, and other medical equipment. The method creates patient-specific pieces.
Its Benefits:
Its parts have many advantages. Key advantages include:
- It creates complicated pieces with outstanding surface finishes. In automotive and consumer product industries, part appearance is crucial.
- Dimensional accuracy: It ensures part fit and operation.
- Cost-effective: It is economical for low-volume production. It creates parts without expensive tooling, saving time and money.
- Polyurethane, silicone rubber, and epoxy can be vacuum cast. This adaptability allows for parts with diverse properties and characteristics.
Conclusion
It provides high surface detail, dimensional accuracy, cost-effectiveness, and adaptability. Automotive, aeronautical, medical, and consumer products use it. Traditional manufacturing processes cannot create complicated pieces with fine details like this process can. It is a cost-effective and efficient approach to make high-quality products.
It is basic and easy to learn. It’s affordable for smaller businesses and startups that can’t afford pricey tooling and production runs.
It is extremely adjustable, providing for versatility in part design and attributes. This is useful in aerospace and medical industries where parts must be adapted to specific applications and environments.
Reference
*Image from https://handk-heisengp.co.jp/